NIKKEN Service Capabilities
Our dedicated service team are at the heart of our business, assisting our customers in maintaining product longevity and ensuring all our solutions perform to the renowned NIKKEN standard.
All NIKKEN engineers are time served and have regular and intensive training sessions backed by our Japan Headquarters, ensuring they are up to date with the latest products. As opposed to 3rd party repair companies, the NIKKEN service department focus solely on NIKKEN / Elbo Controlli NIKKEN products and are the only team in the UK to receive the latest information on upgrades and new models direct from the NIKKEN factory.
With a combined experience of over 150 years, our team benefit from a vast skill set that covers all aspects required to maintain and repair NIKKEN products. Our engineers are qualified to perform a variety of mechanical and electrical tasks, including minor repairs, major overhauls & full refurbishing with powder coating, fault diagnosis and onsite support.
If I had to give one tip to customers, it would be to make sure that you have your Rotary Tables / Presetters serviced by NIKKEN every year. Not only are we the OEM using genuine parts to retain the quality NIKKEN is known for, but the experience and knowledge of our products is simply unrivalled. Opting for preventive maintenance will always prove to be more cost effective when compared to a ‘if it isn't broken don't fix it’ approach – your car needs servicing every year, and so does your Rotary Table / Presetter!
Tim Bruce, Assistant General Manager - NIKKEN Euro-Centre
Service Capabilities:
- Rotary Table / Presetter servicing with reports & certificates for your ISO:9001 records
- Full Presetter calibrations - geometry checks and adjustment, if needed
- Repairs on NIKKEN Rotary Tables, Presetters, Tooling and Alberti Angle Heads
- Full functionality & condition checks
- Adjustment of backlashes etc. where appropriate
- Oil change and resealing of covers to prevent coolant ingress
- Presetter software upgrade (if a later version has become available)
- Supply & fitting of new cable looms
- Free serial number check for information on the history of the table
- Refurbished tables available to purchase
- Organise service schedules / plans. Recommended service intervals & annual reminders.
- Check for evidence of non-genuine parts fitted
- Check the wiring is configured to NIKKEN standards
NIKKEN HEALTH CHECK
Recently had a 3rd party repair you’re unsatisfied with? Please let us know and we may be able to offer a FREE health check.
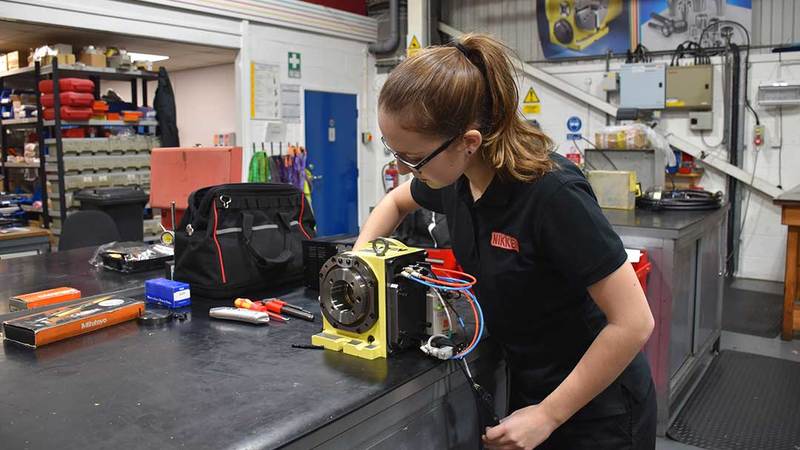
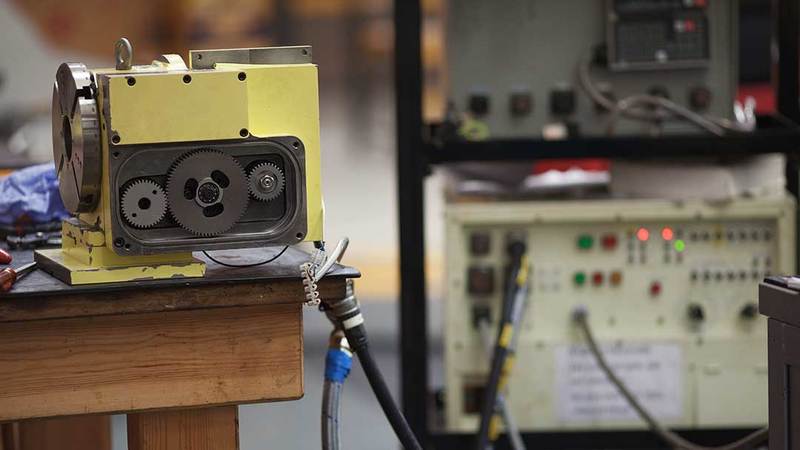