How does it differ presetting on a machine compared to with a presetter?
Presetting Tools: How Off-Machine Solutions Boost Efficiency on the Shop Floor:
In today’s highly competitive manufacturing environment, maximising machine tool uptime is critical. One of the most often-overlooked factors impacting productivity is the method used for tool presetting- the essential process of establishing tool length and diameter offsets before machining operations can commence.
Traditionally, setting tools directly on the machine has been standard practice. Operators use methods such as touching the tool to the workpiece, using a gauge, or employing probes and lasers to determine offsets. While effective, these procedures come at a significant cost: time. Every minute spent setting tools inside the machine is time lost from actual metal cutting- the activity that ultimately generates revenue. Even with automated systems to measure and set twenty to thirty individual tools, one by one in the spindle for a given operation or process, can take anything between ten to thirty minutes- during which time the machine of course remains idle.
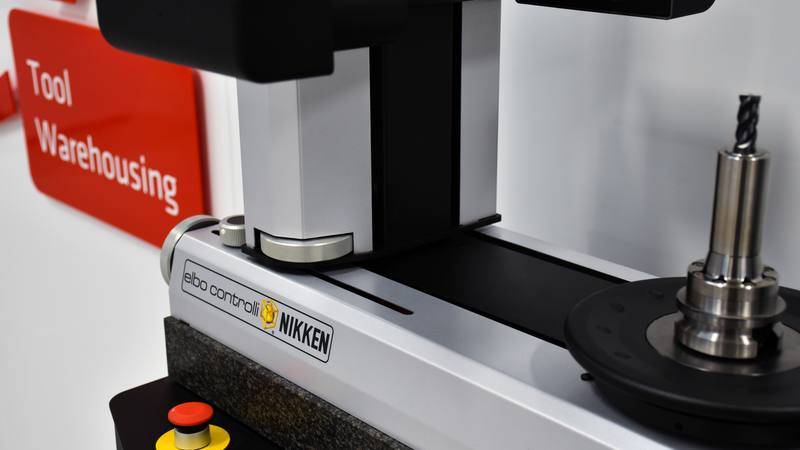
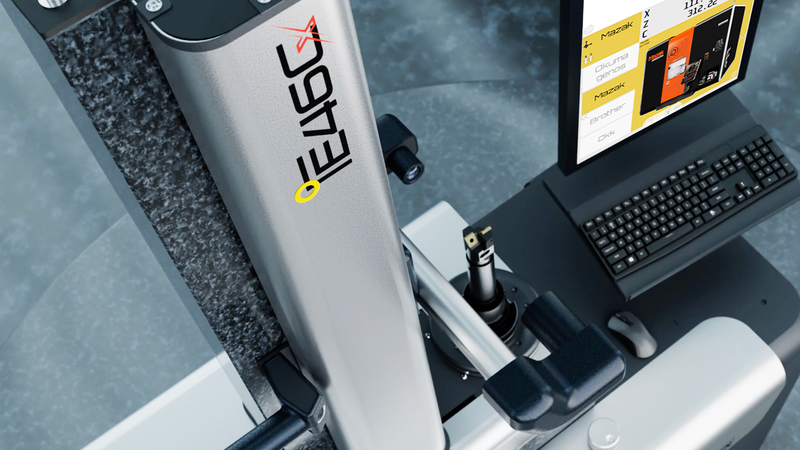
Advantages of using a Tool Presetter:
-
Free Up Your Machines
Move tool presetting outside the cutting area so your machines can focus purely on metal cutting. -
Boost Productivity
One external presetter can serve multiple machines- dramatically improving workflow. -
Save on Setup Costs
On-machine setting systems can cost £2,000-£4,000 per machine. External presetters are a smarter investment. -
Work Smarter, Not Slower
Prepare tools while machining is underway- no more waiting between setups.
Why NIKKEN Presetters are the one to help boost productivity, reduce machine downtime and increase performance.
Our new automatic Tool Presetters feature:
- Patented automatic spindle rotation
- Enhanced user interface
- Semi-autonomous axis movement
- Built for precision and ease of use.
Increase your ROI!
Unlock more jobs, maximise machine utilisation, and grow your bottom line.