Cost Effective Solutions for Batch Productivity
Perhaps the most well-known solution for batch applications is a trunnion assembly. Introducing one to a CNC platform allows for multiple loading of numerous components in one setup. NIKKEN provide a range of adaptable 4th Axis Rotary Tables and TAT support combinations to ensure there are no limitations when it comes to the size of the component.
NIKKEN’s standard modular trunnion assemblies are available in a range of lengths to meet most demands (500mm, 750mm and 1000mm as standard). Precision manufactured using a choice of steel or aluminium our solutions are perfect for practically every machine tool and bed length and capacity. All our standard trunnions are designed and available to mount and fit directly on to our compact rotary table ranges which include the NCT200, CNC202 or the CNC260 (others can, of course, be adapted to meet any such requirement). To increase the scope of any trunnion set up NIKKEN can also provide various choices and options for work holding to allow diversity and adaptability for different parts and components.
One popular and proven solution that has been supplied to many customers is to incorporate a rail system on to the trunnion plate which can potentially allow for 6-sided machining. This option and capability massively increase productivity. Effectively multiple components can be loaded on either side of the trunnion but mounted on opposing faces. This allows for 3 sides to be machined on one face of the trunnion and the remaining 3 sides on the next face (operation one and two in a single set up).
This is a typical example of such a setup. Four components are held and machined together with two parts coming off finished each time the cycle is completed. This allows the machine to run longer and gives the operator the opportunity and scope to carry out additional work in the cycle.
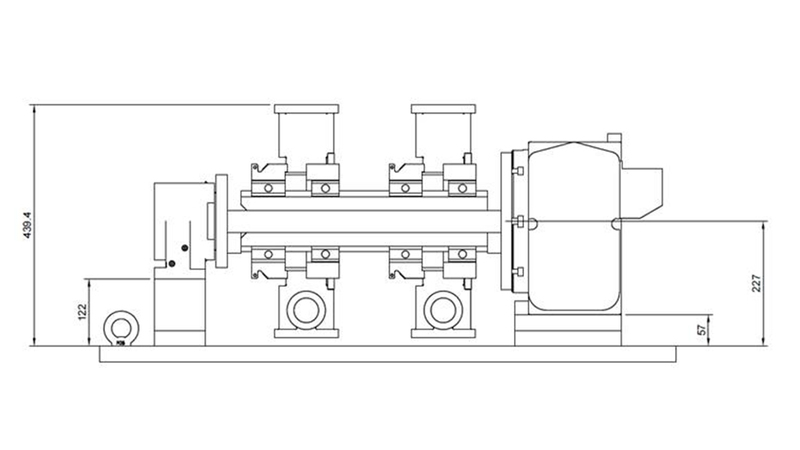
Application Study
A recent installation at TWM Technology perfectly demonstrates the incredible power and benefits of multiple part loading with a trunnion. Originally machining a total of 28 components per day the company chose to invest in a trunnion solution which led to an incredible increase to 224 components per day! Ultimately this solution eliminated the potential requirement for the customer to have to purchase more machinery to meet demands.
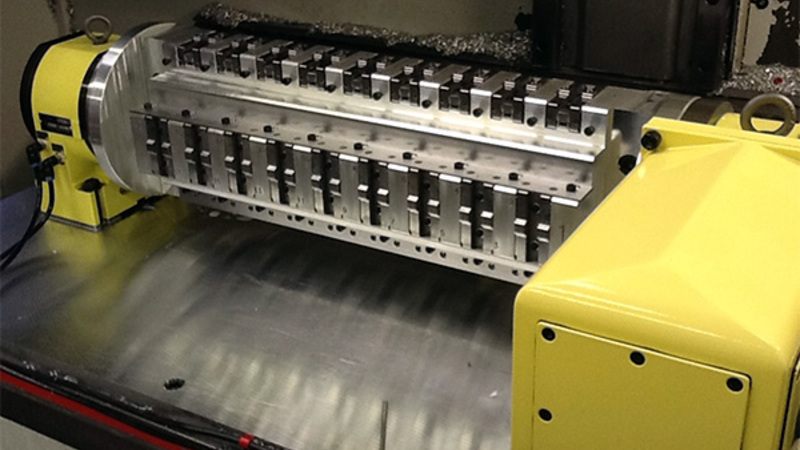
For smaller components, NIKKEN has a complete range of compact multi-face Trunnion solutions. These, along with the ability to provide both single-axis and twin axis rotary tables with up to 4 spindle outputs, can substantially increase machine uptime. Though actually increasing the running time of the total process by introducing multiple spindles, compact multi-face trunnion plates and supports (where necessary) it is possible to considerably reduce the effective cycle time and cost of individual parts and components.
Our rotary tables and solutions can play a massive role in improving efficiency for production!
Any machine tool can benefit from an additional axis. A single-axis table (CNC) adapted for multi loading allows the ability to present more components to the machine spindle in a single cycle. By adding a twin axis table (5AX) the machine tool in question is instantly capable of five-sided machining in a single operation. This reduces the setup time, helps to eliminate loading error and therefore contributes to additional potential savings in respect of reworking and scrap.