Straight Line Engineering, Nelson, Lancashire
Established in 1979, Straight Line Engineering is a leading supplier of precision tooling for any hot or cold forming process. Allied but not limited to the aerospace industry, they have experience in the design, project management and manufacture of many forms of impression based tooling.
Servicing companies in high-precision industries such as aerospace places special demands on suppliers to deliver exacting quality standards. Straight Line were experiencing issues with the surface finish on components and reduced tool life, which they thought was down to the performance of their existing ER Collet chucks, and invited NIKKEN to investigate and provide a solution.
NIKKEN, together with engineers from Straight Line, quickly identified an application where this was particularly apparent and set about addressing the issues. Forming tool components being machined were suffering from inaccurate profiles and sub-standard surface finish, being caused by tool deflection due to the poor performance of existing ER Collet Chucks. This became apparent before the Carbide cutting tool life had expired, resulting in the need to replace cutting tools way before necessary. To overcome the issues with the finish, components had to undergo an additional flat honing, blending and polishing process to meet production tolerances, which increased production time and reduced efficiency.
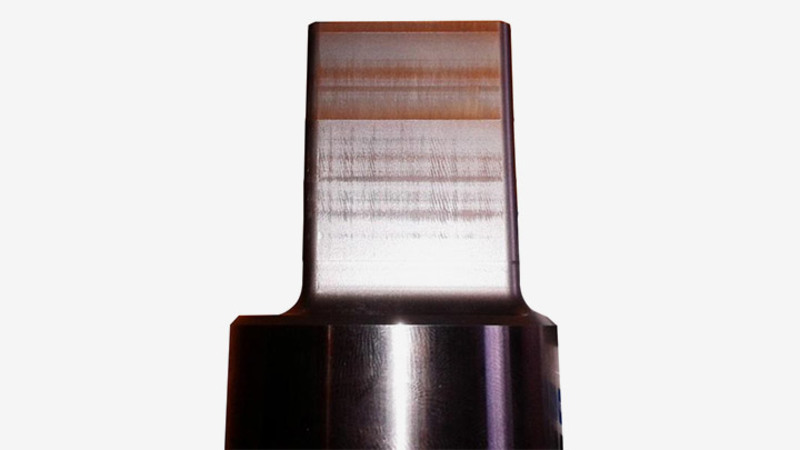
Photograph above shows the physical steps left by cutter deflection. Carbide tool held in ER style chuck. This component would require flattening, blending and polishing
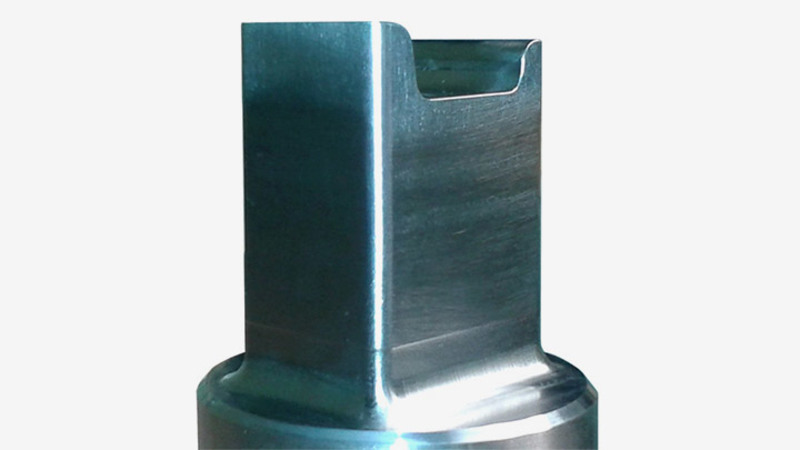
Photograph above shows component with correct finished geometry. Carbide tool held in Nikken Slim Chuck. This component would not require flattening, blending or polishing
The solution offered by NIKKEN was to replace the offending ER collet chucks with NIKKEN Slim Chuck tool holders. The performance gains were immediate, with zero tool deflection machining times were reduced and the profile and surface finish achieved required no further finishing process. Tool life was also increased, with the additional benefit of a previous polishing process no longer being a requirement.
These performance increases are directly related to the superior design features included in the NIKKEN chuck design. Adopting an 8 degree taper and flat shoulder pushing method on the Collet results in double the gripping power of a 16 degree tapered face ER collet design, with no risk of the collet “rocking” in the tool holder. This results in a highly accurate, precise and secure clamping method, delivering unbeatable results in over 1 million applications globally.
Remarking on the results, Andrew Greenwood from Straight Line Engineering said:
Aside from the improvements identified in this project there are far more implications involved, changing to a NIKKEN balanced chuck on this application has achieved an improvement across the board
Andrew Greenwood, Straight Line Engineering
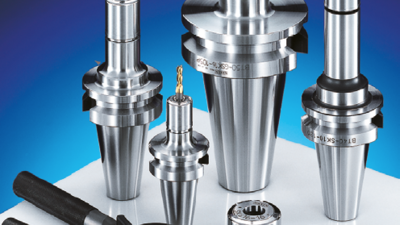
NIKKEN Slim Chuck Product Range