5-Axis Capability at Cambridge Precision Limited
When Cambridge Precision Limited needed to expand their production capacity they had a choice, either a dedicated 5-Axis machine tool or a vertical machining centre with a separate, fully integrated 5-Axis rotary table.
After critically evaluating alternative solutions the decision was made to purchase a Doosan Vertical Machining Centre with a fully integrated NIKKEN 5AX-201 Rotary Table, a solution that stood “head and shoulders above the rest” commented Richard Hobbs, Cambridge Precision Managing Director. “One of the main reasons for going down this route is the flexibility this solution gives us; with the 5-Axis table at one end it is possible to do simple 3 Axis work whilst the table is still in situ, and if the full machine bed is needed the Table can be removed easily.”
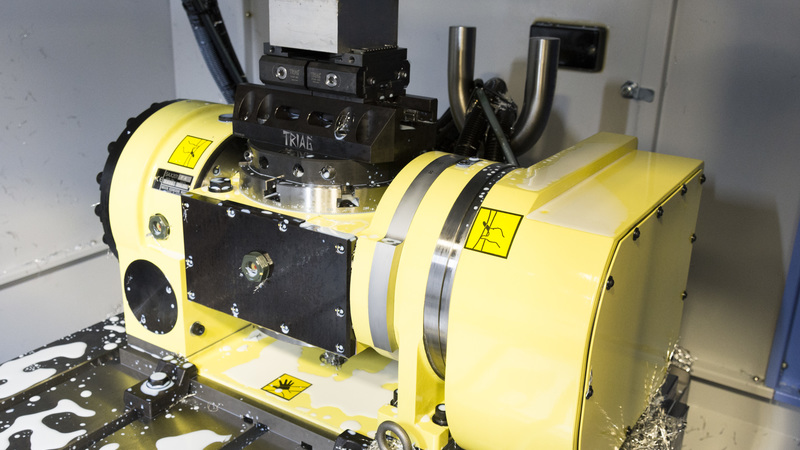
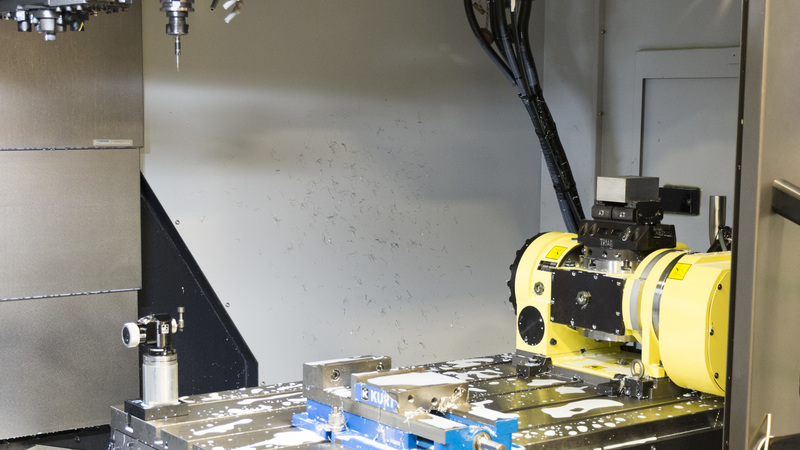
Full 5 Axis machining capability had been on the horizon for some time and the decision was made to implement the technology after visiting an Open House event at the newly opened NIKKEN Innovation Centre Europe (NICe) in February 2016.
The first step was to install a NIKKEN 5AX-201 on an existing Machining centre, with full integration being carried out by NIKKEN to provide true full 5-axis simultaneous machining capability.
In addition to the superb quality of the NIKKEN products their service has been second to none – “we like to deal in facts and NIKKEN have a straight-forward no-nonsense approach to doing business. All the solutions and approaches that have been recommended have performed exactly as we expected, combine this with an excellent product and you have a winning relationship that is sure to last for a long time” commented Richard.
Whilst process efficiency and one-hit manufacture sound great, only when the impact on business is realised can the true value can be demonstrated. Cambridge Precision have been manufacturing a particular component for a customer for a number of years, but due to economic reasons the work was put out to China to cut costs. This move, although attractive on paper, soon proved to be unsuitable for a number of reasons and the customer approached Cambridge Precision to see if anything could be done to improve the efficiency and reduce costs. Thanks to the 5-Axis capabilities that had been introduced, the part which used to be produced in multiple set-ups on a horizontal milling machine could now be manufactured in one operation in less than a quarter of the time on a vertical machining centre.
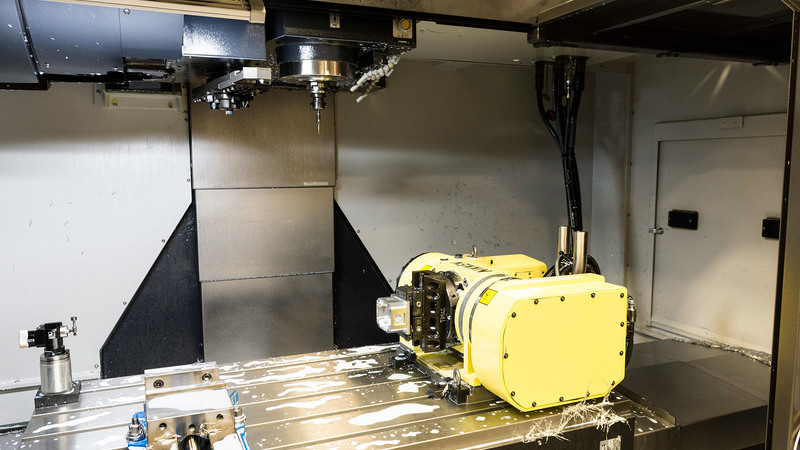
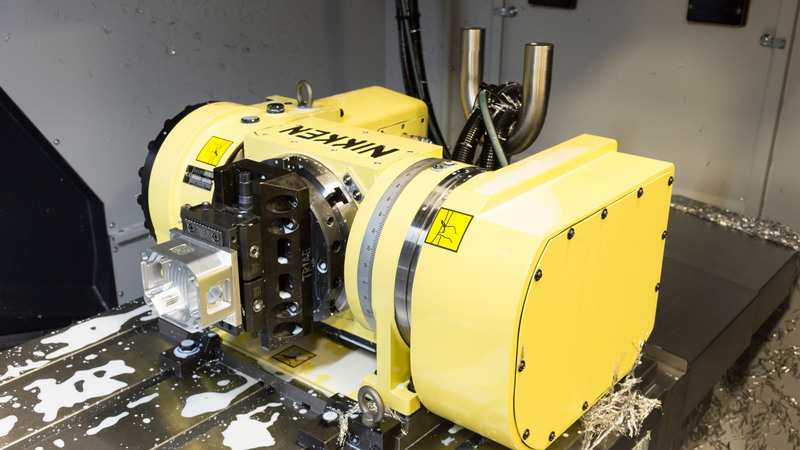
The result of this single process improvement is that the manufacture of a component and the subsequent supply-chain value has been re-shored to the UK, safeguarding jobs and staying ahead of the curve thanks to the application of technology and best practice.
The implementation of full 5-Axis machining has been a real eye-opener for the engineers at Cambridge precision – components that would have previously been manufactured in multiple set-ups to include turning and milling operations are now manufactured in a single operation, cutting the cycle time dramatically. “Having the 5-Axis functionality on our machine tools means that you can tear up the rule books” said Production Manager Nick Raven. “Things I learned as an apprentice engineer have been turned on their head – we can now achieve the same geometry and tolerances by approaching the job in a totally different way, cutting down on the number of set-ups and dramatically reducing cycle times.”
The increase in workshop productivity has led to the need for off-line programming to be implemented for the companies’ three CNC Coordinate Measuring Machines. “With the increase involume and complexity of components being produced we have had to invest in the effectiveness of our inspection facilities” said Richard. “Batches of components that used to take days to produce are now completed in a few hours, with improved levels of accuracy thanks to the repeatability of the NIKKEN Rotary tables”.
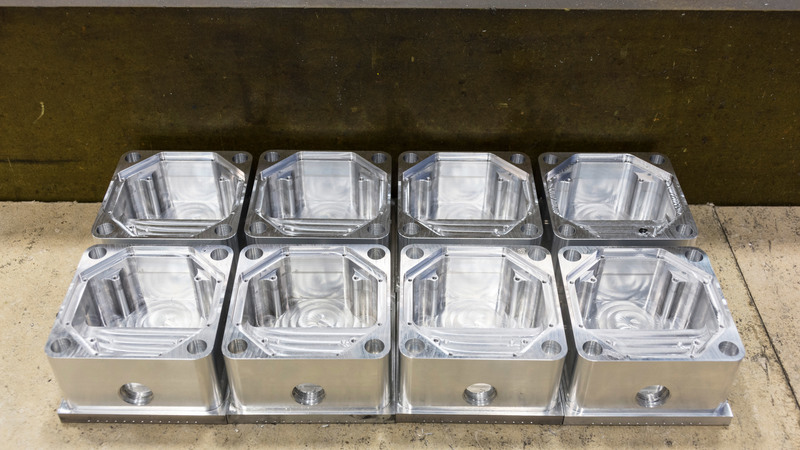
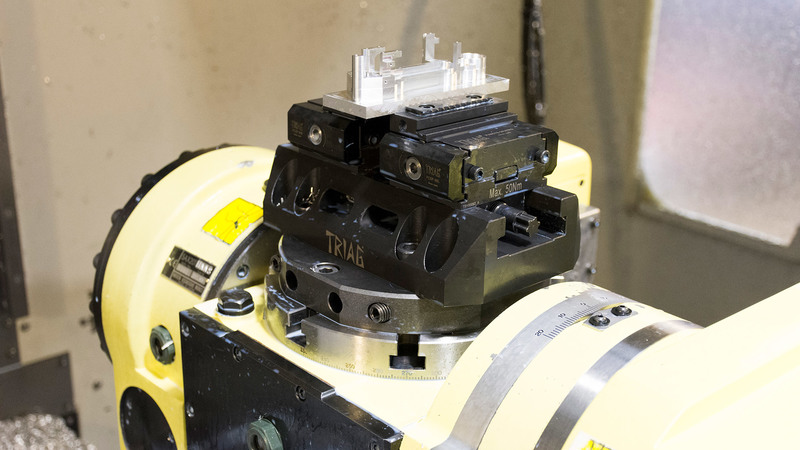
Moving forward the opinion of the Cambridge Precision management team is that every new machine tool put in place will have a 5-Axis capability, “the flexibility of having a standard vertical machining centre with 5-Axis capability means that we can respond to customer demands quickly and provide the fastest turnaround possible on even the most complex components – why would we consider anything else?”
Cambridge Precision have recently been granted “Fit for Nuclear” status, recognising them as having the required level of excellence in their processes to bid for work in the civil nuclear supply chain. This, together with a total commitment to quality and best practice, meant that they are well placed to take advantage of the continued demand for high quality precision machined components.
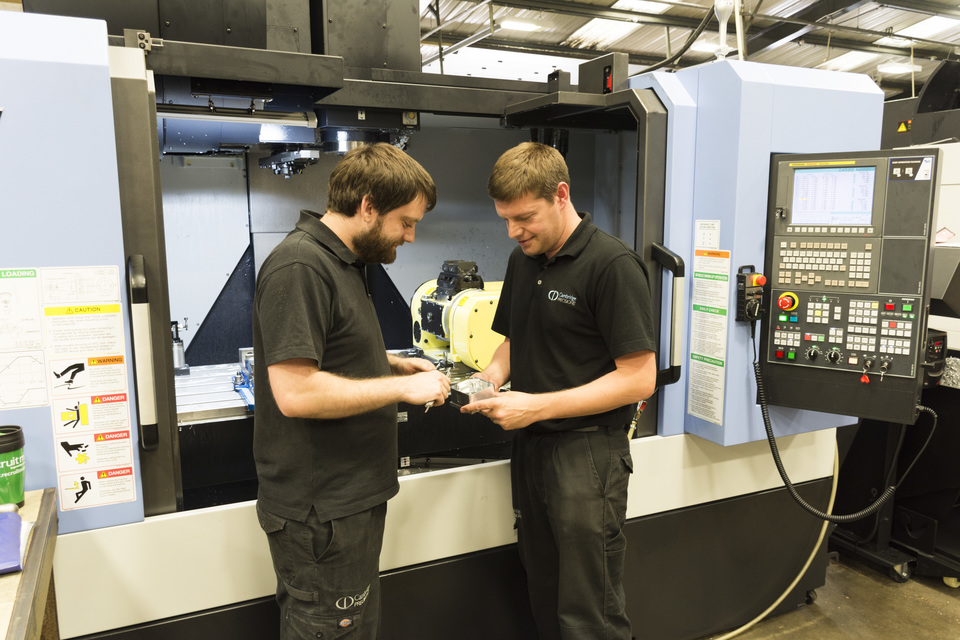