Reduce Operating Time and Increase Stability with an Alberti Angle Head
An established specialist in high quality precision engineering recently contacted NIKKEN to support a project they were working on in the Czech Republic. The job at hand required multiple tooling for one operation, however they knew that with an angled head they could potentially achieve this in one operation.
The company initially attempted to use a competitor angle head from a Czech supplier; however, this did not meet their standards.
A spokesperson added:
The angle head wasn’t good enough at all. You could hear the gears grinding as you were machining with it clearly demonstrating a lack of construction rigidity and stability. It also proved near impossible to consistently maintain the correct angle without adjustment.
Having previously worked with NIKKEN, the company knew that our solutions were reliable and offered high-accuracy and performance, prompting them to contact their local Business Manager for an alternative solution.
The NIKKEN technical department designed a stopper block to suit the Mazak spindle and ensured the safety of the tool change by using a 3D printed arm which replicated the proposed angled head. This allowed the team to check every eventuality from clearance issues inside and around the machine tool carousel whilst also predicting possible tool problems before the head is even ordered and installed.
Having visited the NIKKEN Innovation Centre for a live demonstration, the company chose to invest in an Alberti Angle Head which their local Business Manager helped install. Since the installation, the company have experienced a reduction in operating time for the initial component from around 3-4 minutes down to only 10 seconds!
A spokesperson added:
We came to NIKKEN because we knew they were the best, from the product to the support from the team.
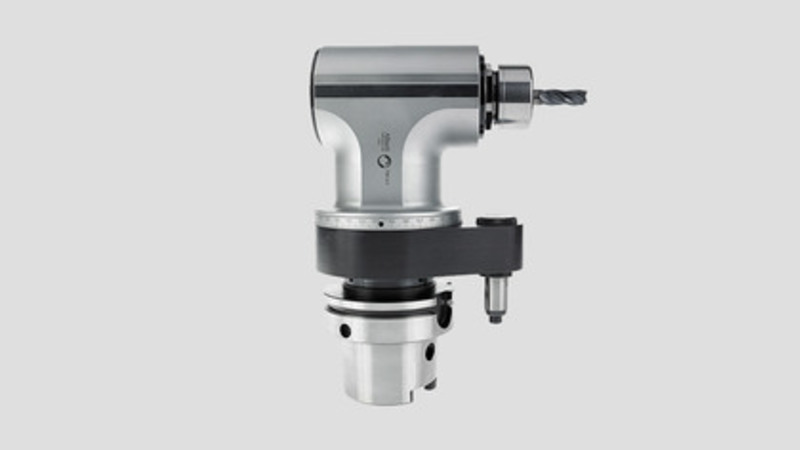
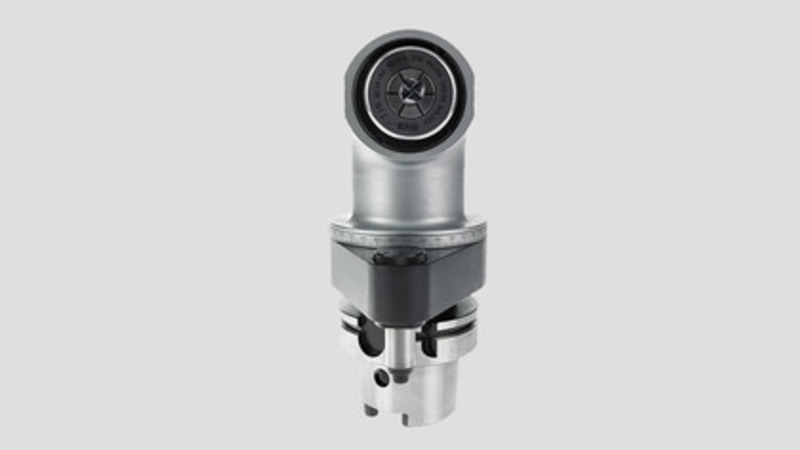