IIDEA Ltd
Acclaimed for their diverse service offering, IIDEA Ltd provide market-leading precision engineering, specialising in a range of design, machining & metallurgical solutions including CAD/CAM, CNC milling & turning, sawing & metallurgy expertise.
Located at the Advanced Manufacturing Park, South Yorkshire, IIDEA supply to a broad range of sectors, ranging from power and energy, oil and gas, motorsport, materials testing and development, and other sport and leisure.
With the recent installation of a brand new VMC to increase their capacity for high-speed machining, IIDEA have partnered with local design company True Components to manufacture high end bicycle components, specifically speed sensor mounts for the renowned HPS-Systems (www.ride-hps.com) creators of the lightest production electric bicycle in the world.
While originally some of these parts were created in the far east, True Components recently decided to relocate production to Sheffield, citing the quality and reliability synonymous with manufacturing in the Sheffield City Region.
To guarantee the components fulfilled and succeeded expectations on quality, IIDEA utilized a range of NIKKEN solutions throughout the process. Employing the best-selling NIKKEN 5AX-201 Rotary Table with a Triag Work Holding system for ultimate grip and versatile multi-axis capability, IIDEA ensured the complex parts could be machined quickly and with the highest precision.
We wanted a machine with a decent table size but also with multi-axis capability, the solution best suited to us was to have a 3-axis VMC with a trunnion table mounted on one end of the bed. We wanted a table that would be highly accurate and also last a long time, so NIKKEN was the obvious choice.
When assessing the correct tooling required for the job, NIKKEN’s reputation for quality solutions and comprehensive support played a big factor, with the Innovation Centre also based at the AMP offering technical assistance whenever required. These factors led IIDEA to select a range of NIKKEN face and taper contact Multi-Lock and Slim Chuck solutions, citing the incredible gripping force and reliability that can be achieved across a variety of materials and machining processes. This combination of NIKKEN solutions has ensured impressive surface finishes, process security and accuracy.
We can be machining complex aluminium parts at high speed and feed rates one day, then extremely tough nickel alloy parts the next. NIKKEN tooling is ideal for this as it provides excellent gripping force and reliability whilst also being capable of running at high spindle speeds.
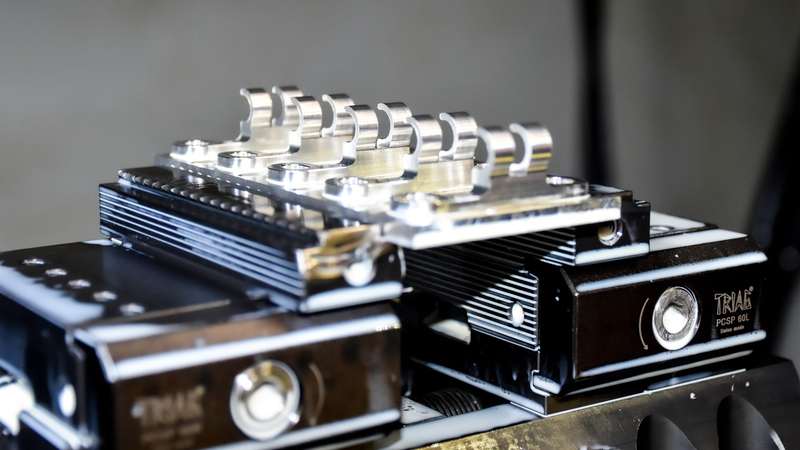